Pain Point
The current operational challenges are multifaceted. Manual order processing from the seller center is time-consuming, exacerbated by difficulties in tracking warehouse issues due to the absence of dedicated customer service. Infrequent stock checks, limited stock connection between OMS and seller center, and the lack of WMS API accessibility add complexity. Moreover, the OMS lacks support for virtual bundles, and excessive extra costs for handling, including labeling and infrequent stock checks, further compound the issues. Additionally, the absence of video packing support from the warehouse adds another layer of constraint to the existing operational inefficiencies.
Solution from Titipaja
Streamlining operations is essential, focusing on four key aspects. Firstly, integrating Warehouse Management System (WMS) with Order Management System (OMS) enhances overall efficiency. Secondly, a robust API integration ensures seamless communication between systems. Thirdly, implementing measurable productivity and quality processes is vital for sustained improvement. Lastly, maintaining accurate stock levels and adhering to Service Level Agreements (SLAs) aligned with marketplace standards are pivotal for operational excellence.
Result
Our partnership with Titipaja has been a game-changer. The automated order processing ensures efficiency, and the ease of tracking and resolving warehouse issues has significantly improved. Conducting stock opname twice a year enhances accuracy, and the strides made in stock connection have been commendable. The open API in our Warehouse Management System (WMS) facilitates seamless integration, and the Order Management System (OMS) now supports bundling processes. The flexibility in cost charging has streamlined our financial operations, and the inclusion of a video guide for the packing process adds an extra layer of transparency and reliability to our collaborative efforts.
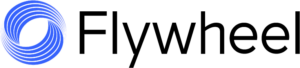
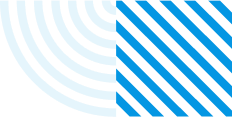